What we do
Products / Material

Our company name Steka already contains an important reference to our main raw material steatite, because Steka stands for steatite ceramics. Steatite is a ceramic material based on magnesium silicate, the starting material is soapstone, which is found in nature. The special properties of steatite, such as high mechanical strength and electrical insulation properties, make it suitable for the production of components with particularly tight tolerances.
Steatite is an excellent ceramic material for dry pressing processes and is particularly gentle on tools. Depending on the application, Steka manufactures products from other porous and non-porous ceramic materials. Together with our partners from Hungary to Japan, we develop individual innovative solutions for our customers. We will be happy to advise you on the right choice of material for your desired application.
Engineering and development
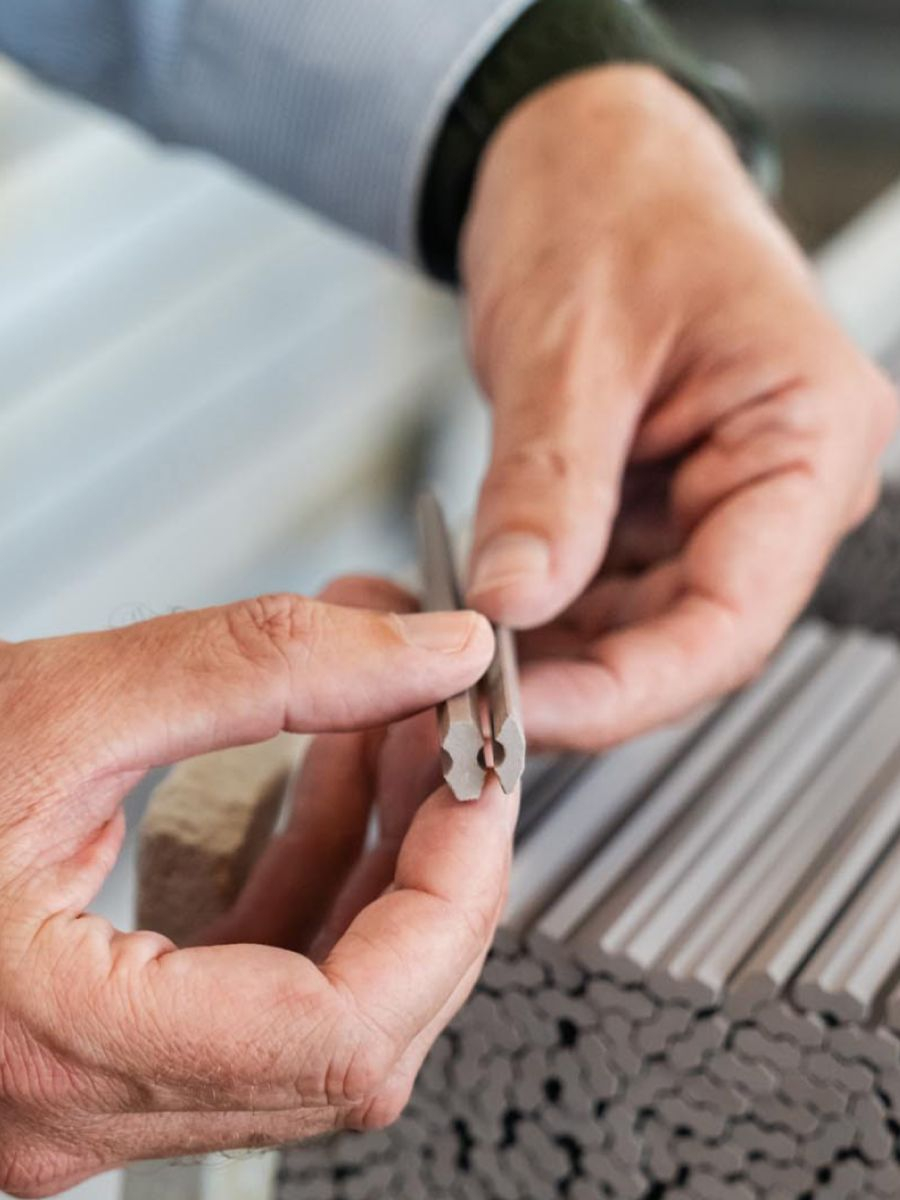
We are happy to take on any new challenge to achieve the best possible result in the interests of our customers. Our long-standing, well-trained employees from three generations have a unique pool of experience that focuses on creative and fast solutions. We support you in the development of prototypes and manufacture your orders from small quantities to large series.
Design and development
If you as a customer have an idea and need support in implementing it with the right ceramic solutions, we are exactly the right contact for you. You do not need to bring along a finished design or a drawing for the desired component.
As a first step, we will sit down with you to understand the exact functionality of the component or your product. Thanks to our decades of experience, we can proactively contribute our ideas right at the start of the process to provide you with the best possible support in choosing the optimum form and function for your product. Because we have a genuine interest in your product and its optimization!
Research and development
As Steka, we regularly work together with renowned universities and research institutes in Austria and Germany. These collaborations have already led to the development of numerous innovations for our customers' products.
An example of this is the K-Regio project "Optimized ceramics/ New areas of application for sintered materials through model-based optimization of competing technical requirements: Strength - thermal conductivity - mass transfer"
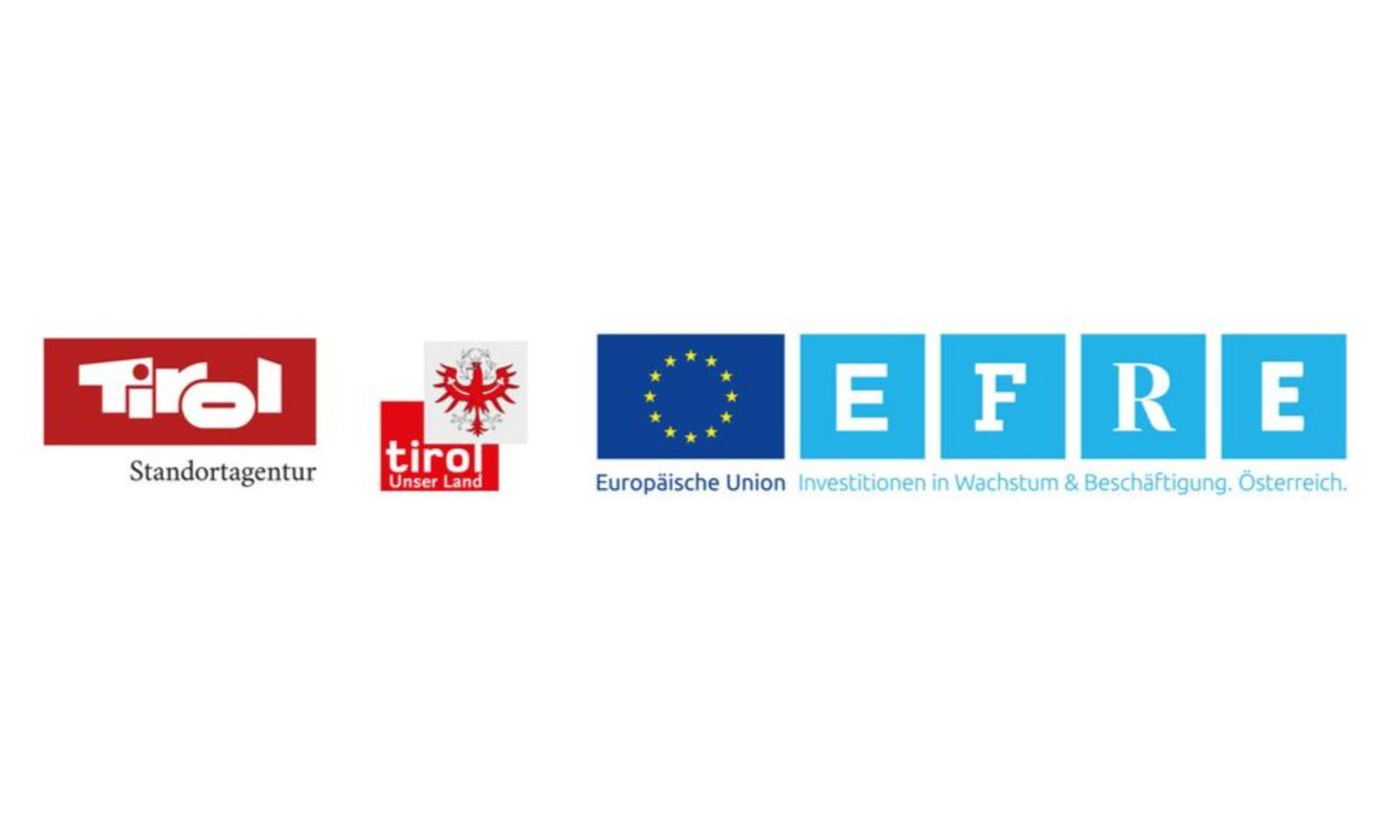
Production
Manufacturing process
Digital fitness / CAD-software we use
At Steka, we work with the latest digital standards and programs. For example, product development and design have access to the latest tools in the field of 3D design programs, such as Inventor and Autocad from Autodesk. Design data is usually exchanged with the development departments of our customers and partners in neutral formats such as .step or .iges as 3D files and .pdf, .dwg or .dxf for dimensioned article drawings with tolerances.
Quality assurance is carried out with the support of the latest CAQ (Computer Aided Quality) software. All production steps are recorded in batches and the test certificates created during the outgoing goods inspection are made available to our customers if required.
Our ERP system supports all areas of the company, from purchasing to dispatch. Production planning and control is also integrated and includes electronic production data acquisition directly at the workstations via an app.
Segments
Over the decades, the Steka product range has continuously expanded. We currently offer our customers more than 1200 different products, from individual solutions to large-scale production. Ceramic materials are used in a wide variety of areas, industries and sectors.
electrical heating
Heating of industrial halls, production facilities or tools as well as components in automotive or medical technology
energy
NH fuses, reduction coils or shunt reactors for a stable power supply, renewable energy e.g. mirror supports for CSP systems
domestic appliances
Temperature control and safety in household appliances, connection technology, connections and protective housings
special solutions
Sensing technology, sensors, automotive technology, bell casting, infrared heating rods, wild bee nesting aids, room fragrance applications and design elements