Company
About
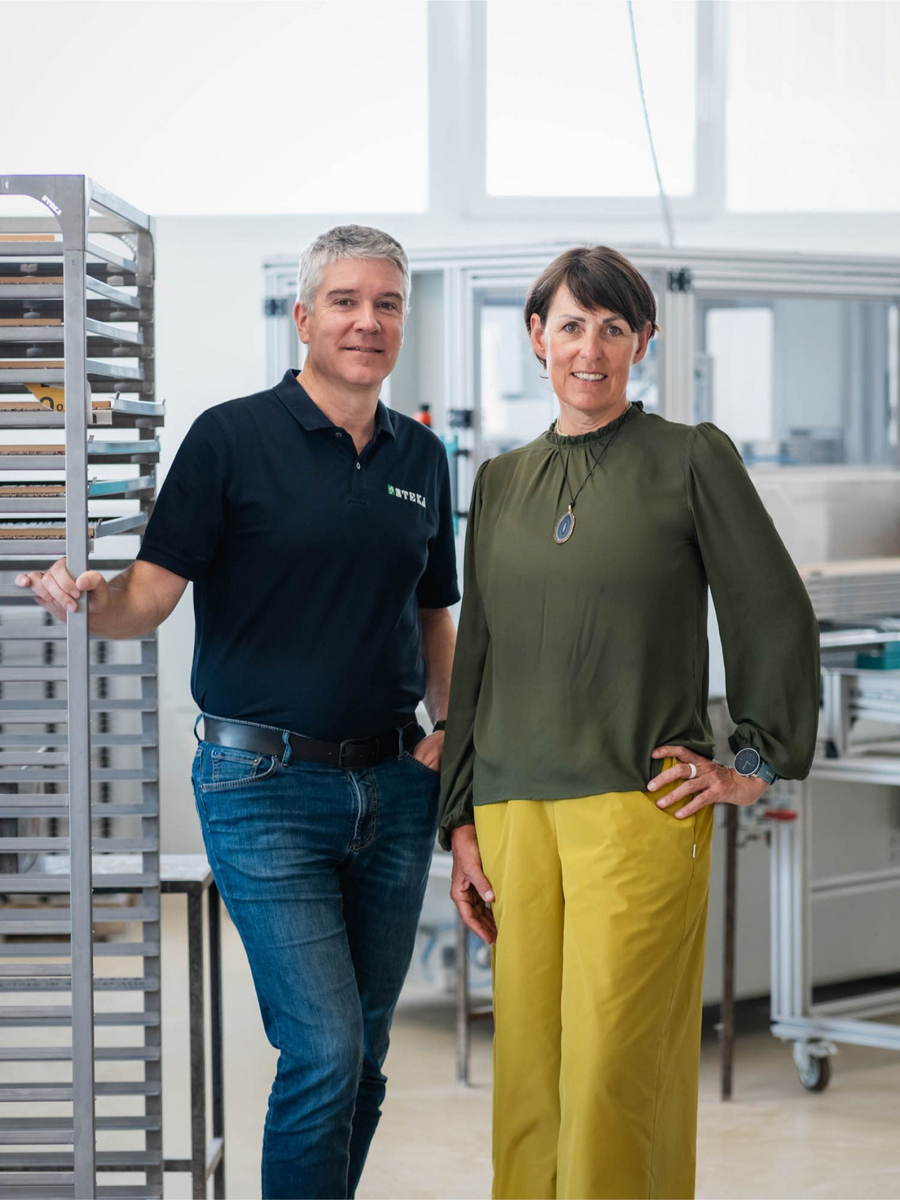
Third generation of management: Markus and Nicola Dax
Today, Steka sees itself as a modern employer that is constantly adapting to the developments of the times. Meaningful work, self-efficacy and regular exchanges between owners and employees are at the heart of the corporate philosophy. Everyone can and should contribute to the company as a whole and thus assume the necessary personal responsibility in a modern company.
Our values
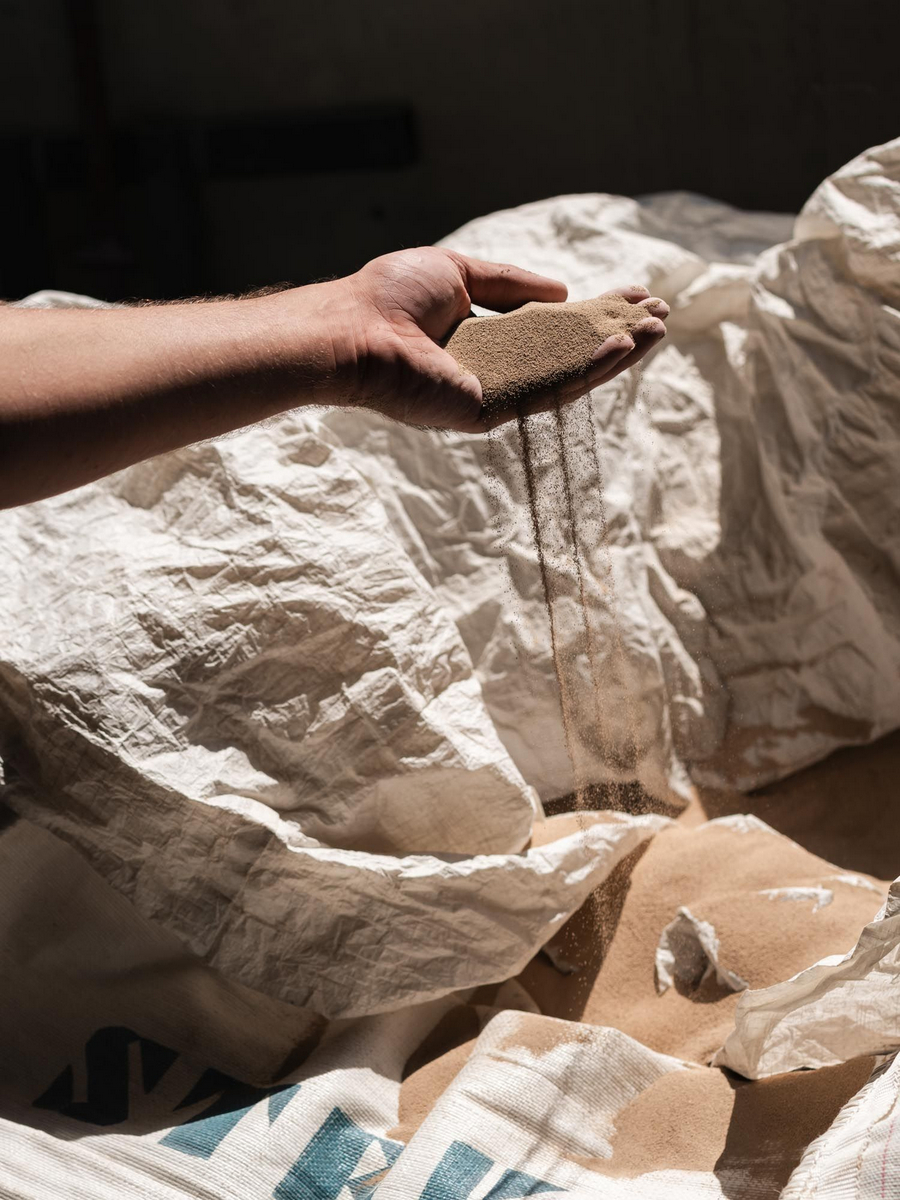
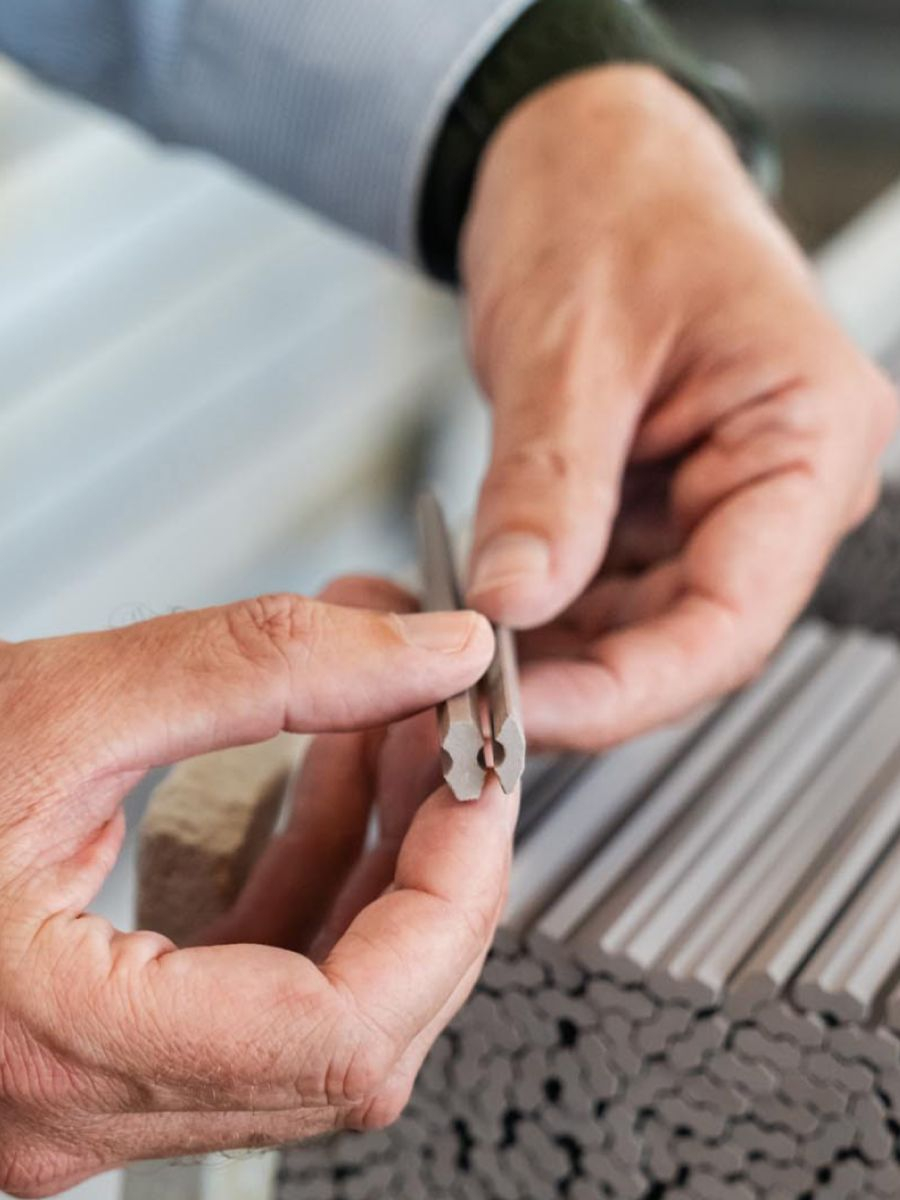
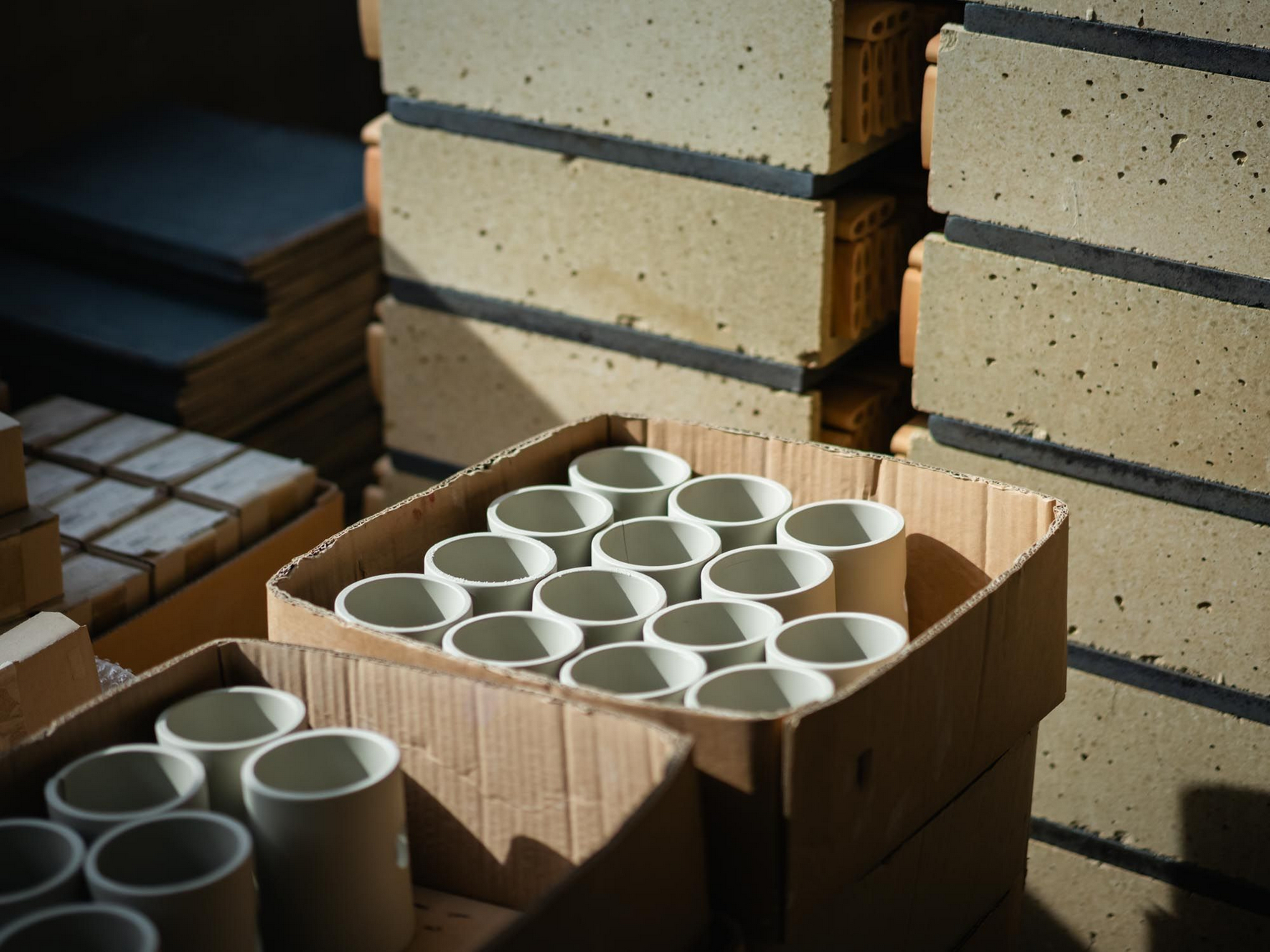
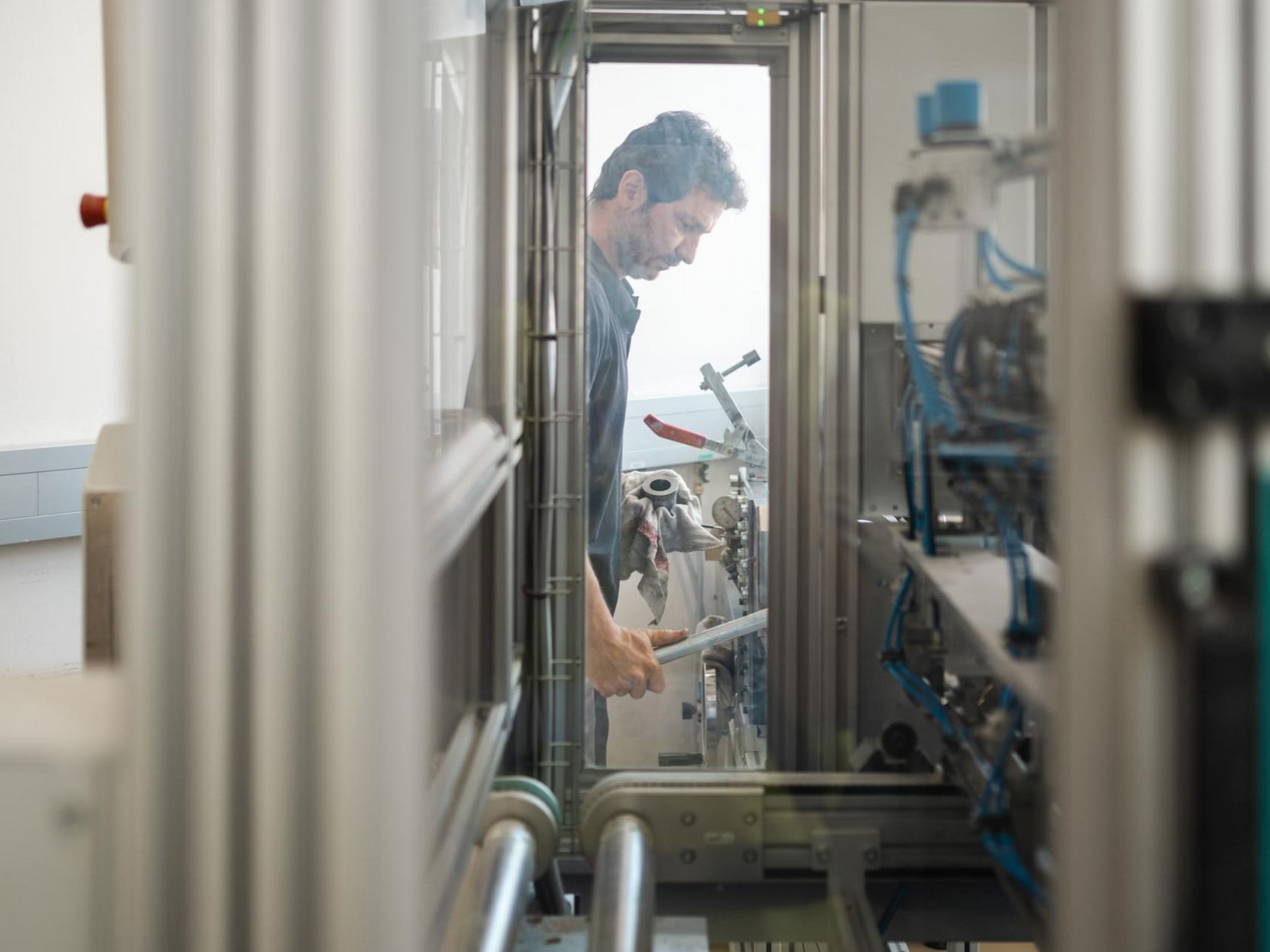
At Steka, we are particularly proud of our strengths and expertise: short communication channels within the company, excellent availability of individual contacts and an extremely committed, highly qualified core team.
All team members, from the production technician to the design engineer and the sales staff to the management and the owners, coordinate their activities on an ongoing basis and are always available for you.
We are hapy to receive your call + 43 512 33402 or to receive your message via Email sales@steka.at.
Company history
75 years of Steka-Werke Technische Keramik
06.10.1949 STEKA, Tiroler Steatit- und Keramikwerke Rojkowski & Co. KG was founded to manufacture components made of high-frequency ceramics and electrical porcelain. There was a lack of electrical fuse cartridges throughout the country. People made makeshift bridges with wires or nails. Accidents and smouldering fires were the result. Swarovski in Wattens built electrical insulating components from ceramic, but saw its own operational future in crystal glass production. In a kind of management buy-out, the head of the department, Ferdinand Rojkowski, was supported in setting up his own plant in Matrei am Brenner. The Dax family was one of the first shareholders. Paul Dax, then a board member of Siemens Tirol, was a customer at the time with a great interest in technical ceramics from local production.
Exports all over the world are booming. Two tunnel kilns are put into operation to cope with the constantly growing demand. 40 tons of technical ceramic components leave the factory every month. In 1959, the site in Matrei becomes too small.
Since 1961, STEKA has been manufacturing in the company building in Innsbruck-Rossau.
The second generation takes over. The father and father-in-law of the current owners, Otto Dax, embarks on a career as a ceramics engineer and, from 1967, develops the company into an export-oriented specialist for the electrical industry that is known far beyond the borders.
Technological developments have characterized STEKA since 1975, keeping the company one step ahead of its Asian competitors.
Attention is always paid to energy efficiency. In 1988, gas-fired chamber kilns with exhaust gas afterburning systems replace the oil-fired tunnel kilns and increase the quality and environmental compatibility of production.
In 1987, the plant is renamed STEKA-Werke technische Keramik GmbH & Co. KG. Steatite is the inspiration for the company name STEKA, Tiroler Steatit- und Keramikwerke. Steatite belongs to the group of silicate ceramics and is ideal for all components in electrical and radio engineering. It consists of a high proportion of soapstone and only vibrates minimally when exposed to electricity or radio waves. As a result, the material does not heat up and hardly changes its expansion - ideal for applications in areas where the tightest tolerances must be maintained.
From 1993, STEKA engineers develop semi-automatic production equipment for ceramic components in metal composites, such as riveted lamp bases. Setting devices for automatic presses allow several machines to be operated by one person.
Since July 2011, Markus Dax and his wife Nicola Dax have been managing the company following the untimely death of Otto Dax, a second-generation ceramics engineer who played a key role in shaping the company and establishing international business relationships.
In 2012, Markus and Nicola Dax purchased the last remaining shares in the company held by third parties and have been the sole owners of the company ever since.
With a constant focus on technological, organizational and personnel development, STEKA asserts itself on the increasingly complex international market through the highest quality of its products and through individual, solution-oriented and personal customer support.
Customer requirements, as the original founding mission, are still deeply rooted in the company's DNA. If desired, many years of knowledge about the material and its properties in use are already incorporated in the design phase in cooperation with the customer's development departments. This optimizes the efficiency of the design and manufacturing process.
The company is currently investing in new extraction systems that will contribute to improved air quality at workstations, lower energy consumption and significantly reduced noise emissions.
In the area of product development, Steka is working together with customers on projects such as extremely thin-walled, filigree multi-hole tubes for measurement and environmental technology, porous ceramics for evaporators or components for particle separation in the chimney of wood-burning systems. Ceramic parts are also used in aviation and the increasing use of electromobility, which relies on technical ceramics for electrical insulation.
STEKA currently employs around 50 people exclusively at its plant in Innsbruck and generates an annual turnover of around 5 million euros.